Emulsion Breaking System (EBS)
The emulsion breaking system has been engineered to deliver the best quality separation at the lowest Operating and Maintenance costs. Other technologies can be expensive, noisy, energy consumptive, and do not always work. The EBS works efficiently by maximizing the use of gravity.
Oil Water Separators (OWS) are an effective technology in most oil-water separation applications. However, there are some applications which require chemical conditioning due to the oils being emulsified. Emulsification can be due to the addition of chemicals such as surfactants or excessive mechanical shearing through mixing or passing through pump impeller.
How our Emulsion Breaking System Works
Separating emulsified oil from water can have different applications. Simple demulsification can be achieved by using a technique referred to as Acid-Cracking. By reducing the pH of the wastewater to a range between 2 and 4, the free oil will separate and rise to the surface of the oil water separator.
EllisLudell engineers have responded by designing the Emulsion Breaking System (EBS). The EBS system has two pH chemical reaction tanks (one acidic and one alkaline) to adjust the pH of the wastewater to be in the acid phase to release free oils to separate through the OWS section of the EBS. The acidic wastewater flows to the pH neutralization tank where caustic soda is added to raise the pH to be discharged within local effluent discharge limitations.
Designed to API 421 and 620 standards, EllisLudell engineers will work to select the best model and materials of construction to maximize oil separation.
Oil coalescing media packs are available in different materials to best suit the application needs of cost, wastewater temperature, corrosion resistance, and chemical compatibility.
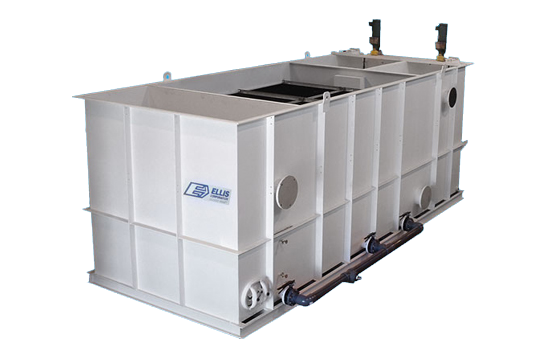
The OWS System Design
The beauty of the OWS design lies within the simplicity. As shown in the figure below the feed enters the OWS on the left (for reference) and is immediately directed downward. The wastestream feed then flows upward through a media pack. Inside the pack the demulsified oil begins to coalesce and float upwards and over a baffle into an isolated oil collection chamber.
Discrete oil globules will rise due to buoyant forces to form an oil layer on top of the water. This makes them relatively easy to remove in an oil water separator (OWS). Free oil can be removed by gravity separation which is what the OWS is designed for. Removal is a function of wastewater flow conditions, differences in specific gravity, temperature, and the stability of the oil. Coarse oily solids with a specific gravity >1.0 will settle to the bottom of conical hopper of the OWS.
Product Options
-
Materials of Construction – 304 Stainless Steel
-
Removable 304 Stainless Steel Coalescing Media Packs for High Temperature and Corrosive Chemicals
-
Solids Discharge Auger
-
Intake and Discharge Pump Packages
-
Vapor Tight Covers and Hatches
-
Controls and Control Panel
-
Intake Heat Conditioning
-
Freeze Protection
-
OSHA Approved Catwalks with Safety Railings, Stairway or Ladder.
Product Features
-
Standard Oil Water Separator with Two pH Adjustment Tanks and chemical mixers
-
Pre-Assembled at Factory Reducing On-Site Installation Time
-
3/16” Thick Carbon Steel Construction
-
Exterior Protection Polyurethane Enamel Paint
-
Coal Tar Coating for interior protection against corrosion
-
Removable ¾” spacing PVC Coalescing Media Packs
-
Covers with Gaskets.
-
Adjustable Weirs for Maximum Oil Separation
-
Level Controls
Emulsion Breaking System Performance
- After Demulsification of the wastewater the EBS Removes Free Floating Oils and Settleable Solids
- Removes 99% of Free-Floating Oils 20-micron sized hydrocarbons and larger
- Produces effluent down to 10 mg/L or less.
Types of Oil Removed
- Motor oils, Fuels (vehicle/jet),
- Fuel oils,
- Hydraulic fluids,
- Immiscible machining oils,
- Lube oil,
- Transmission fluid,
- Bunker c,
- DNAPL,
- LNAPL,
- Vegetable-based oils,
- Crude oil,
- Air compressor lubricants and other Hydrocarbon based derivatives (BTEX etc.)
Applications
-
Centralized Wastewater Treatment Facilities
-
Hazardous Waste Treatment
-
Refineries
-
Vehicle Wash Racks
-
Industrial Process Water
-
Groundwater Remediation
Applications
-
Steel Mills
-
Tank Farms
-
Petro-Chemical
-
Shipping Ballast and Bilge Water
-
Power Generation
-
Heat Treating